线割技术之小孔的 切割方法
1、小孔工件简介工件特点 1.孔小一般在0.8mm以下 2.预孔加工困难 3.补正量不易控制 4.多孔类小孔工件PITCH易走失二﹑预孔加工要求预孔加工难点:1.对刀不准易出现位置偏移导致破孔2.加工中电极摆动易使表面破孔3. 因机台性能关系同条件加工仍有不稳定情况,其不稳定性会引发异常
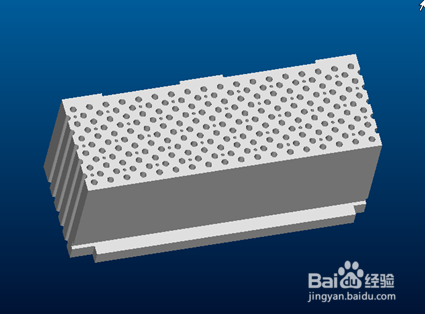
3、二﹑预孔加工要求预孔加工条件选择各机型小孔预孔加工对应加工条件二﹑预孔加工要求预孔加工刳噪受刃条件选择各机型小孔预孔加工对应加工条件二﹑粲崛纫鳍预孔加工要求预孔加工工艺 1. 下料类加工工艺 2. 对刀类加工工艺二﹑预孔加工要求下料类加工工艺 1.料板不宜过大,大小一般在80mm左右 2.料板各面G见光,正角0.01mm以内,厚度余量控制在0.5-1.0mm 3.加工前扫平各面并标示基准, Ø0.5mm及以下孔从背部逃孔至正面2-3mm处, 正面用细电极加工二﹑预孔加工要求下料类加工工艺 4.采用反面逃孔时,正面加工必须和逃孔保持基准一致不错位 5.小孔(使用Ø0.20和Ø0.15mm电极加工)预孔加工必须严格按小孔标准条件进行选择二﹑预孔加工要求对刀类加工工艺 1.工件外形预留0.02-0.05mm余量,以防对刀误差过大及表面腐蚀 2. Ø0.20mm及以下电极加工时,必须采用双边对刀,以保証对刀位置精度 3.多件应采用入孔定位加工,以提高重復定位精度及提升加工效率二﹑预孔加工要求对刀类加工工艺 4.孔径较小时采用背面Ø0.50mm电极逃孔,正面预留2-3mm使用细电极加工,為更好控制逃孔深度,可采取侧面加工工艺孔形式(需经客户同意)电极与预孔大小比照表 对刀类加工工艺 侧面工艺孔形式示意图二﹑预孔加工要求对刀类加工工艺 5.头部段差较大时,则应从背面直接打穿,当难度过大或孔过小时可采用ES加工预孔或与客户协商改善工件结构工艺三﹑程式制作方法凹痕預防干涉預防圓孔程式 1.程式制作使用之程式 2.現場加工使用之程式三﹑程式制作方法凹痕预防 线在过切处因多次放电会使过切处產生凹痕﹐在小孔加工时表现更為明显﹐故需对此状况做事先预防三﹑程式制作方法凹痕预防_改善思路 1.过切距离减小 2.在不同点过切 3.过切处能量减小(粗割)
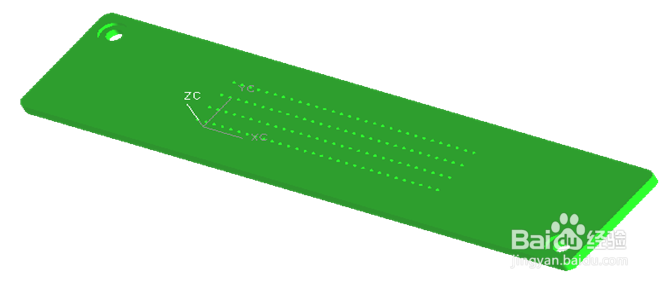
5、三﹑程式制作方法公用圆孔程式 為防止小孔类圆孔加工產生干涉﹐及方便现场人员快速编程和程式人员高效制作程式﹐目前各部门已编写多个公用圆孔程式 如﹕CIRCLE.NC OK2壅酪认奉76.NC YUAN.NC MYC.NC …三﹑程式制作方法 …公用圆孔程式 自编公用圆孔加工程式均為代数程式,它可把每一刀补正值代入NC程式中,不使用G41或G42进行补偿,可避免小孔加工因补正设定导致的干涉现象四﹑线割加工要点1.检查预孔预孔有无打大破孔现象 2.有无多打﹑漏打及打偏现象 3.有无未穿现象 四﹑线割加工要点 实测预孔 加工前必须准确测量预孔大小及位置﹐线割根据预孔状况进行加工﹗ 无论对刀类还是下料类﹐小孔工件加工均必须严格遵循此要求加工四﹑线割加工要点
6、四﹑线割加工要点能量控制 粗割时易断线﹐应适当减弱加工条件以减少断线次数﹐提升加工效率 1.小孔冲水不良(孔径小) 2.小孔预孔生锈(未吹干及未上油) 3.小孔预孔侧壁有突起尖点
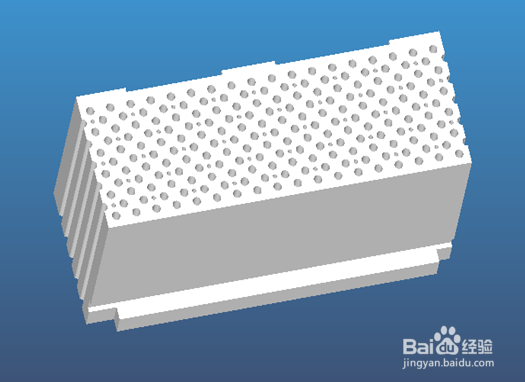